Enhancing Performance and Quality Via Modern Metal Stamping Approaches
As the needs for accuracy and effectiveness continue to escalate, the integration of automation and digital devices right into the steel stamping process has actually come to be vital. By exploring the complex interaction in between innovation, automation, and accuracy in metal marking, a pathway towards unrivaled productivity and quality guarantee unravels.
Benefits of Modern Steel Marking
Modern metal marking deals many advantages in regards to effectiveness, precision, and cost-effectiveness in the manufacturing sector. One of the key advantages of contemporary metal marking is its capability to efficiently generate high volumes of complex steel get rid of consistent high quality. This process removes the requirement for multiple procedures as it can carry out numerous tasks such as blanking, piercing, developing, and reeling in a solitary operation.
In addition, contemporary steel stamping makes it possible for makers to achieve limited tolerances and exact specifications, ensuring that each part fulfills the needed criteria. This high level of accuracy results in marginal material waste, minimized rework, and total enhanced item quality.
Additionally, modern metal stamping is an economical production technique. In essence, modern metal stamping offers a competitive edge to producers looking to improve efficiency and top quality in their procedures.
Advanced Technologies in Steel Stamping
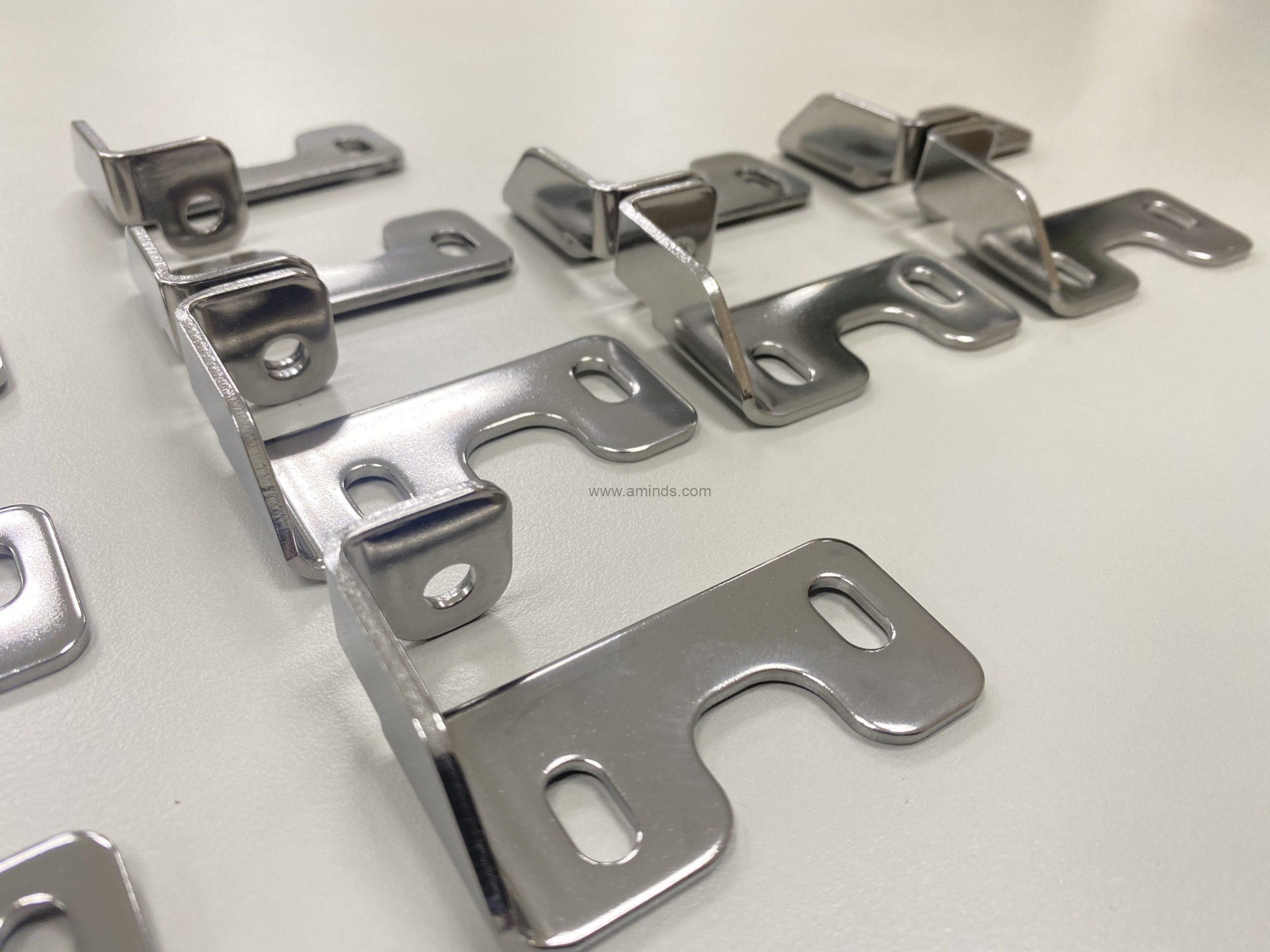
One more key modern technology reinventing metal marking is making use of servo presses. Unlike conventional mechanical presses, servo presses offer better control over the speed and pressure used during the marking process. This control not just improves the quality of the stamped components but additionally decreases material waste and power consumption.
In addition, improvements in simulation software have actually enabled manufacturers to essentially evaluate and maximize the marking process prior to physical production starts. This online prototyping helps recognize prospective concerns early, leading to set you back financial savings and faster time-to-market for new items. In general, these innovative technologies in steel marking are driving unmatched degrees of productivity and high quality in the sector.
Improving Efficiency With Automation
The assimilation of automated systems has substantially boosted the efficiency of steel marking processes. Automation in metal stamping procedures supplies a myriad of benefits, including boosted manufacturing rates, enhanced precision, and lowered labor costs. By utilizing robotic arms and computer-controlled equipment, jobs that were formerly time-consuming and prone to errors can now be implemented promptly and with remarkable precision.
Automated systems have the ability to manage recurring jobs with uniformity, resulting in higher productivity levels and decreased cycle times. This boosted effectiveness not just causes set you back financial savings yet additionally ensures a more streamlined and dependable production process. Additionally, automation permits real-time monitoring and data collection, enabling manufacturers to identify and address issues promptly, further optimizing the total performance of steel marking operations.
Furthermore, automation promotes a safer working setting by lowering the demand for hands-on intervention in hazardous jobs. By passing on these duties to automated systems, workers can concentrate on more facility and value-added tasks, contributing to a more reliable page and effective process in the metal marking market.
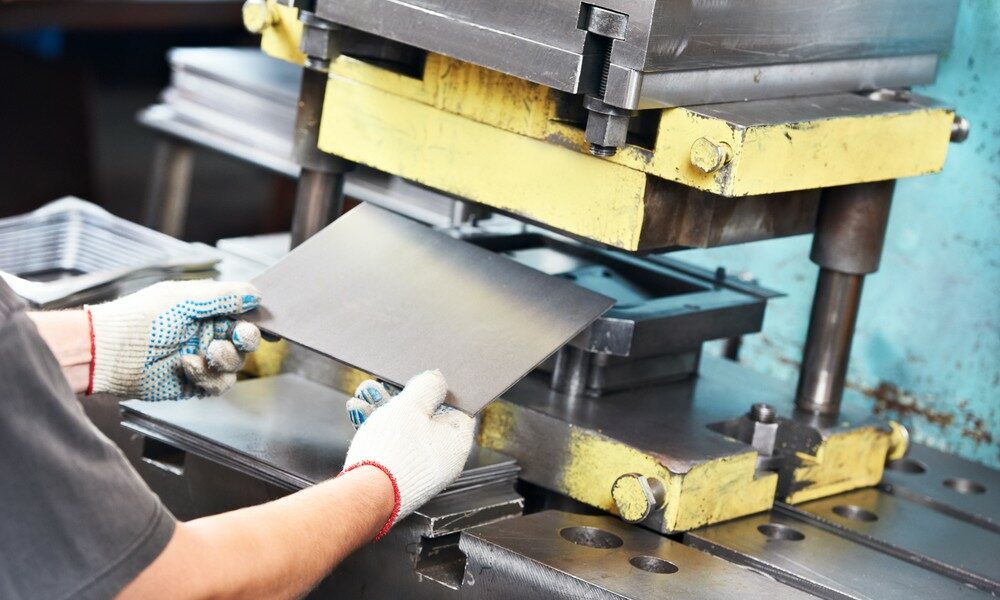
Quality Assurance Measures in Marking
Executing rigid top quality control steps is vital in ensuring the precision and uniformity of steel stamping processes. One of the key quality control steps in steel marking is conducting routine assessments throughout the manufacturing cycle.
Additionally, carrying out innovative technologies such as automated vision systems can even more enhance the top quality control procedure by enabling real-time tracking and detection of any kind of abnormalities throughout manufacturing. These systems utilize video cameras and computer formulas to check components with high accuracy and precision, minimizing the risk of defects leaving into the end product.
In addition, developing a thorough documents system that tapes high quality control data and evaluation results is essential for tracking efficiency patterns and assisting in constant improvement initiatives. By assessing this information, producers can identify possible locations for optimization and execute corrective activities to improve the overall quality of their stamped items.
Enhancing Precision With Digital Tools
Using digital devices can substantially improve the precision of steel Your Domain Name stamping procedures, reinventing the way suppliers accomplish accuracy in their manufacturing. Digital devices such as computer-aided design (CAD) software application permit the creation of detailed stamping layouts with exceptionally precise dimensions. By inputting comprehensive requirements into the software program, makers can ensure that each stamped item Clicking Here meets precise dimensional requirements, minimizing mistakes and waste in the production procedure.
Additionally, the assimilation of sensors and real-time tracking systems in marking devices makes it possible for producers to very closely monitor the marking procedure and make immediate modifications to make certain accurate outcomes. These electronic tools supply beneficial data on variables such as pressure, rate, and alignment, enabling for fast recognition and correction of any type of inconsistencies from the desired specs.
Final Thought
In conclusion, modern steel marking approaches use many benefits for improving productivity and quality in manufacturing procedures. These technologies in steel stamping not only streamline manufacturing procedures however also ensure regular and high-grade outcomes - Metal Stamping.
Comments on “Metal Stamping Processes: From Prototyping to Mass Production”